CNC Turning Parts Factory: The Backbone of Precision Manufacturing
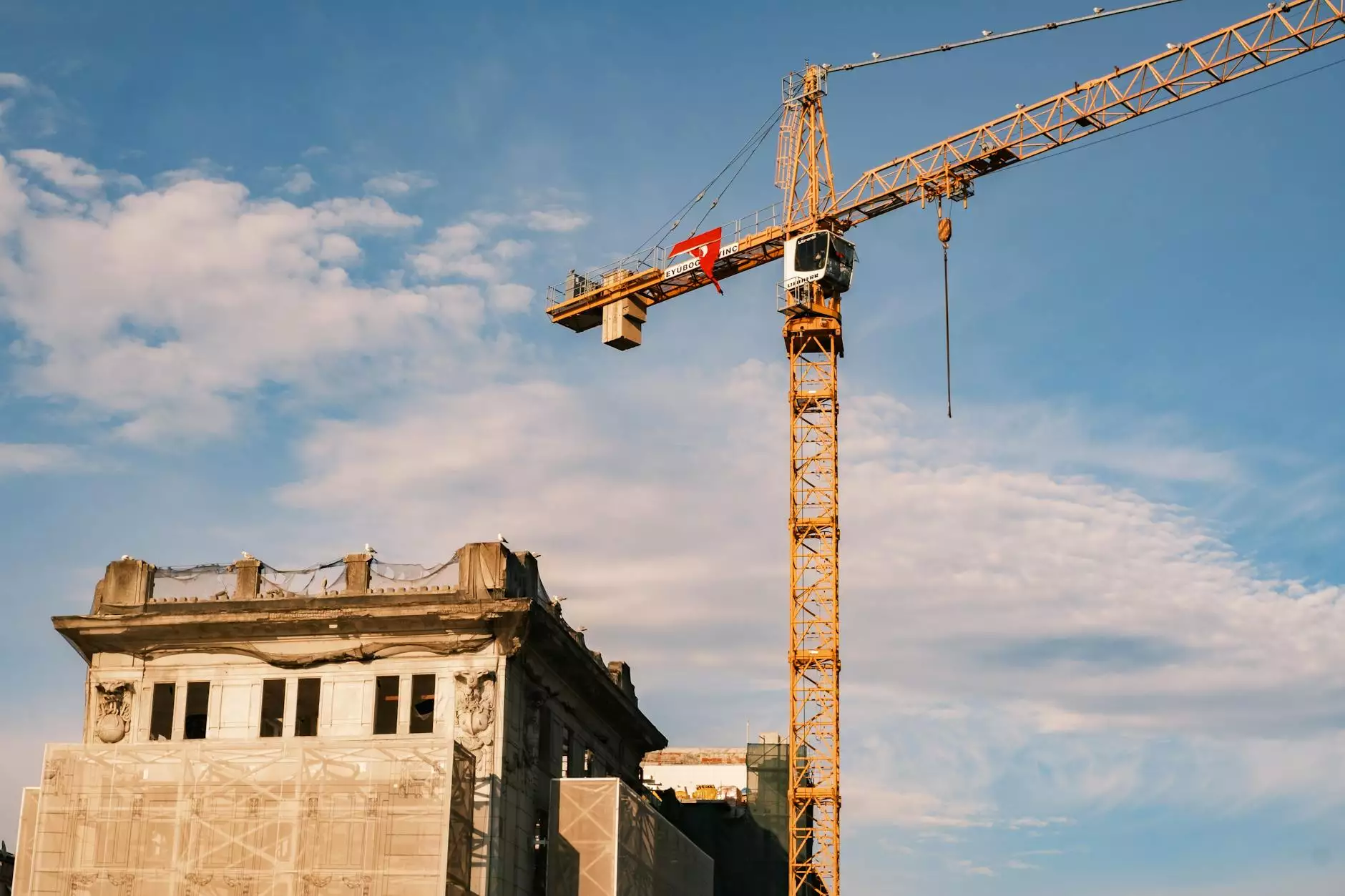
The manufacturing landscape has evolved dramatically over the years, with technology playing a pivotal role in this transformation. One essential pillar of this innovation is the cnc turning parts factory, where precision meets efficiency. This article delves into the intricacies of CNC (Computer Numerical Control) turning, elucidating its importance in metal fabrication and its substantial impact on various industries.
Understanding CNC Turning
CNC turning is a manufacturing process that involves rotating a workpiece against a cutting tool to create cylindrical parts and components. Unlike traditional manual machining, CNC turning is entirely automated, allowing for high precision and repeatability. The operations typically occur on a CNC lathe, where the part is fixed in place while the cutting tool is dynamically moved along multiple axes to achieve the desired shape and finish.
Core Advantages of CNC Turning Parts Factory
- High Precision: CNC turning offers unparalleled accuracy, which is essential for parts that require tight tolerances.
- Efficiency: Automation drastically reduces production time, leading to increased output without compromising quality.
- Flexibility: CNC machines can be easily reprogrammed, allowing manufacturers to adapt to different designs and specifications quickly.
- Consistency: Automated processes ensure each part produced is identical, crucial for mass production.
- Cost-Effectiveness: While initial setup may be costly, the efficiency and reduced labor costs lead to lower overall production costs.
The Role of CNC Turning in Metal Fabrication
The cnc turning parts factory is integral to the metal fabrication industry. These facilities utilize CNC turning for a variety of products, ranging from simple cylindrical components to complex, multi-featured parts. This section outlines the various applications of CNC turning in metal fabrication:
1. Automotive Industry
In the automotive sector, CNC turned parts are ubiquitous. They include drive shafts, brackets, and gears, all of which benefit from the precision and durability of CNC processes. By ensuring that these components meet strict safety and performance standards, manufacturers can produce vehicles that are both reliable and efficient.
2. Aerospace Components
Safety and accuracy are paramount in the aerospace industry. CNC turning provides the means to produce critical components such as fuel nozzles, compressor blades, and housings with an accuracy that other manufacturing methods cannot match. The stringent requirements of this industry necessitate the advanced capabilities offered by CNC technology.
3. Medical Devices
The medical field also relies heavily on precisely engineered components that are often produced in a CNC turning parts factory. Devices such as surgical instruments, implants, and microsurgical tools require exact dimensions and high-quality finishes to ensure functionality and patient safety. CNC turning helps manufacturers achieve these specifications consistently.
Technological Innovations in CNC Turning
The ongoing evolution of CNC technology continues to enhance the capabilities of CNC turning operations. Here are some of the latest innovations being embraced by modern-day cnc turning parts factories:
- Multi-Axis Machining: Modern CNC lathes often feature multiple axes, allowing for the machining of complex geometries in a single setup, significantly reducing the need for part repositioning.
- Automated Tool Change Systems: These systems reduce downtime between machining operations by automatically swapping out dull tools for sharp ones, enhancing efficiency.
- Enhanced Software: Advanced CAD (Computer-Aided Design) and CAM (Computer-Aided Manufacturing) software streamline the design and programming processes, allowing for quicker turnaround times.
- IoT Integration: The Internet of Things (IoT) allows for real-time monitoring of machine performance and predictive maintenance, thereby preventing unplanned downtimes.
Quality Control Measures in CNC Turning
Ensuring high-quality output is critical in a CNC turning parts factory. Implementing stringent quality control measures is essential, and the following practices are standard in the industry:
1. Rigorous Inspection:
Parts produced in a CNC turning facility undergo thorough inspections using calibrated measuring tools and machines like Coordinate Measuring Machines (CMM). These inspections confirm that dimensions meet the required specifications before parts move to the next stage of production.
2. Statistical Process Control (SPC):
SPC techniques help monitor and control production processes by using statistical methods. By analyzing data, manufacturers can detect and correct variances, ensuring consistent quality over time.
3. Certification Compliance:
Many industries require compliance with specific standards, such as ISO 9001. A CNC turning parts factory must maintain such certifications to reassure clients of their commitment to quality.
Environmental Responsibility in CNC Turning
As the demand for sustainable manufacturing practices rises, cnc turning parts factories are adapting to these eco-conscious trends. Manufacturers are implementing various green technologies, including:
- Reducing Waste: By utilizing advanced CNC technologies, manufacturers can minimize material waste, ensuring that more of the raw material is transformed into finished products.
- Recycling Metal Chips: The byproducts of the turning process, such as metal chips, can be collected and recycled, lessening the environmental footprint and increasing cost savings.
- Energy Efficiency: Modern CNC machines are designed to consume less energy, and manufacturers invest in renewable energy sources to power their facilities.
Choosing the Right CNC Turning Parts Factory
When selecting a cnc turning parts factory, several factors must be considered to ensure that you partner with a reliable provider:
1. Technical Expertise:
Evaluate the technical capabilities of the factory, including their experience with the specific materials and designs you require. A skilled workforce is crucial for achieving the precision and quality you need.
2. Quality Assurance Processes:
Inquire about the quality assurance processes in place. A factory that adheres to strict quality standards and possesses relevant certifications will likely deliver superior products.
3. Flexibility and Capacity:
Ensure that the factory can handle your production volume and can adapt to changing requirements, whether you need small prototypes or large production runs.
4. Communication and Support:
Effective communication can significantly influence the overall success of a project. Look for a manufacturer that provides comprehensive support throughout the production process.
Conclusion: The Future of CNC Turning Parts Factory
The cnc turning parts factory represents a vital component of the modern manufacturing industry. As technology continues to advance, the efficiencies, precision, and innovation that CNC turning offers will only become more pronounced. From automotive to aerospace, the applications of CNC turning are vast and varied, meeting the needs of evolving industries.
Choosing the right CNC turning factory is essential for businesses looking to enhance their production capabilities while maintaining high-quality standards. Based at deepmould.net, we are committed to excellence in CNC turning and metal fabrication, offering tailored solutions that meet the specific requirements of various industries.
As we move further into the future, the role of CNC turning will continue to expand, driving excellence in manufacturing while ensuring sustainability and environmental consciousness.